Welding is a process in which two or more kinds of the same or different materials are joined together by bonding and diffusion between atoms or molecules
The method to promote the bonding and diffusion between atoms and molecules is heating or pressing, or heating and pressing at the same time
Classification of welding
Metal welding can be divided into fusion welding, pressure welding and brazing according to the characteristics of its process
In the process of fusion welding, if the atmosphere is in direct contact with the high-temperature molten pool, the oxygen in the atmosphere will oxidize metals and various alloy elements. Nitrogen and water vapor in the atmosphere will enter the molten pool, and defects such as pores, slag inclusions and cracks will be formed in the weld during the subsequent cooling process, which will deteriorate the quality and performance of the weld.
In order to improve the welding quality, various protection methods have been developed. For example, gas shielded arc welding is to isolate the atmosphere with argon, carbon dioxide and other gases to protect the arc and pool rate during welding; For example, when welding steel, adding ferrotitanium powder with high oxygen affinity to the electrode coating for deoxidation can protect the beneficial elements such as manganese and silicon in the electrode from oxidation and enter the molten pool, and obtain high-quality welds after cooling.
Bench type cold welding machine
The common feature of various pressure welding methods is to apply pressure during welding without filling materials. Most pressure welding methods, such as diffusion welding, high-frequency welding and cold pressure welding, have no melting process, so there are no problems like melting welding, such as burning of beneficial alloy elements and invasion of harmful elements into the weld, which simplifies the welding process and improves the safety and health conditions of welding. At the same time, because the heating temperature is lower than that of fusion welding and the heating time is shorter, the heat affected zone is small. Many materials that are difficult to be welded by fusion welding can often be pressure welded into high-quality joints with the same strength as the base metal.
The joint formed during welding and connecting the two connected bodies is called a weld. During welding, both sides of the weld will be affected by welding heat, and the structure and properties will change. This area is called heat affected zone. During welding, the workpiece material, welding material and welding current are different. To deteriorate the weldability, it is necessary to adjust the welding conditions. Preheating, heat preservation during welding and post welding heat treatment at the interface of the weldment before welding can improve the welding quality of the weldment.
In addition, welding is a local rapid heating and cooling process. The welding area cannot expand and contract freely due to the constraint of the surrounding workpiece body. After cooling, welding stress and deformation will occur in the weldment. Important products need to eliminate welding stress and correct welding deformation after welding.
Modern welding technology has been able to produce welds with no internal and external defects and mechanical properties equal to or even higher than those of the connected body. The mutual position of the welded body in the space is called the welded joint. The strength of the joint is not only affected by the quality of the weld, but also related to its geometry, size, stress and working conditions. The basic forms of joints include butt joint, lap joint, T-joint (positive joint) and corner joint.
The cross-sectional shape of the butt joint weld depends on the thickness of the welded body before welding and the groove form of the two connecting edges. When welding thicker steel plates, grooves of various shapes shall be cut at the edges for penetration, so that welding rods or wires can be easily fed in. Groove forms include single-sided welding groove and two-sided welding groove. When selecting the groove form, in addition to ensuring full penetration, factors such as convenient welding, less filler metal, small welding deformation and low groove processing cost should also be considered.
When two steel plates with different thicknesses are butted, in order to avoid severe stress concentration caused by sharp changes in cross-section, the thicker plate edge is often gradually thinned to achieve equal thickness at the two joint edges. The static strength and fatigue strength of butt joints are higher than that of other joints. Welding of butt joint is often preferred for connection under alternating and impact loads or in low-temperature and high-pressure vessels.
The lap joint is easy to prepare before welding, easy to assemble, and small in welding deformation and residual stress. Therefore, it is often used in site installation joints and unimportant structures. Generally speaking, lap joints are not suitable for working under alternating load, corrosive medium, high temperature or low temperature.
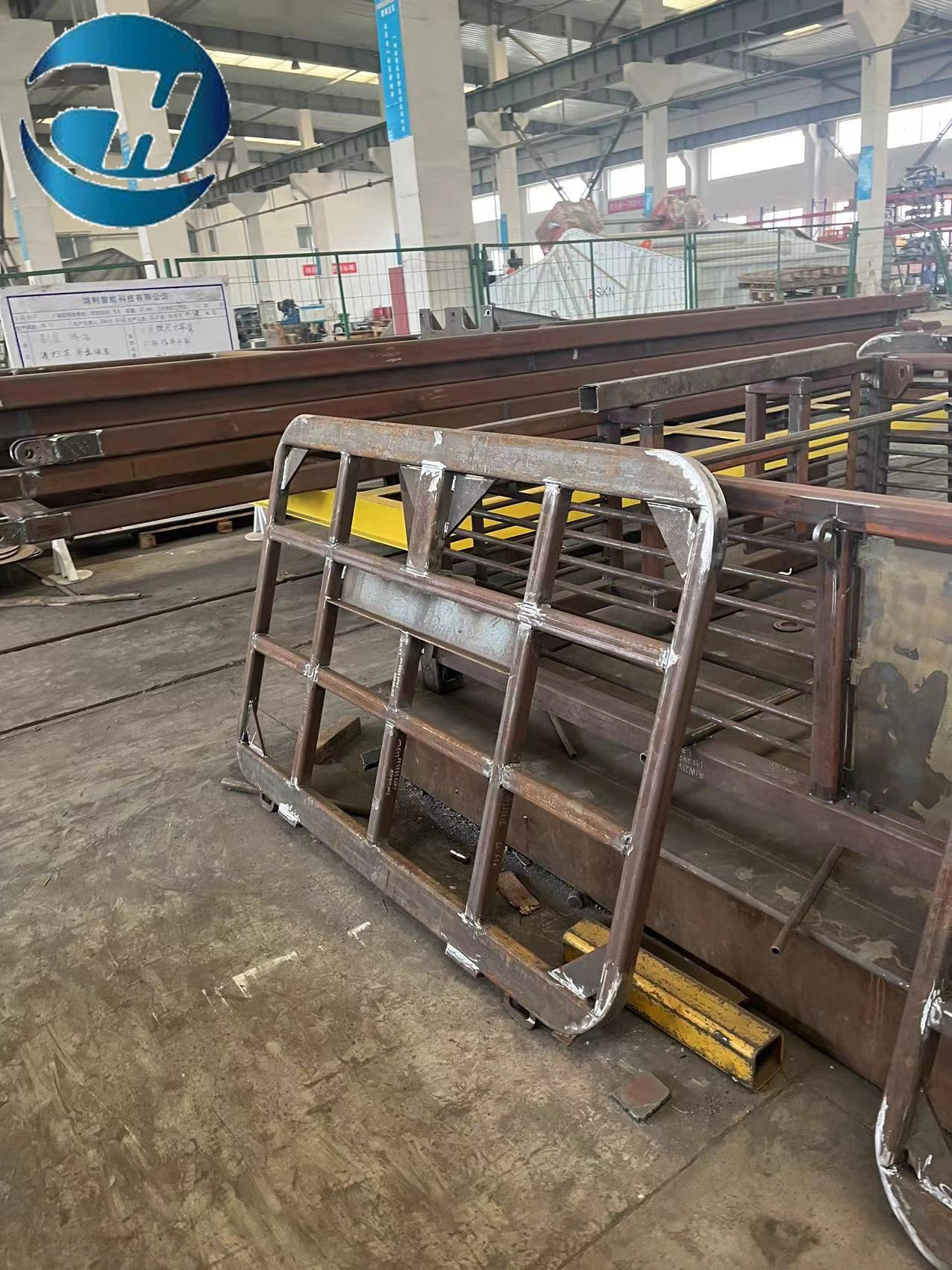
The use of T-joints and angle joints is usually due to structural needs. The working characteristics of incomplete fillet welds on T-joints are similar to those of lap joints. When the weld is perpendicular to the direction of external force, it becomes a front fillet weld, and the surface shape of the weld will cause stress concentration in different degrees; The stress of fillet weld with full penetration is similar to that of butt joint.
The bearing capacity of the corner joint is low, and it is generally not used alone. It can be improved only when there is full penetration or when there are fillet welds inside and outside. It is mostly used at the corner of the closed structure.
Welded products are lighter than riveted parts, castings and forgings, which can reduce the dead weight and save energy for transportation vehicles. The welding has good sealing property and is suitable for manufacturing various containers. The development of joint processing technology, which combines welding with forging and casting, can make large-scale, economical and reasonable casting and welding structures and forging and welding structures, with high economic benefits. The welding process can effectively use materials, and the welding structure can use materials with different properties in different parts, so as to give full play to the advantages of various materials and achieve economy and high quality. Welding has become an indispensable and increasingly important processing method in modern industry.
In modern metal processing, welding developed later than casting and forging, but it developed rapidly. The weight of welded structures accounts for about 45% of the steel output, and the proportion of aluminum and aluminum alloy welded structures is also increasing.
For the future welding process, on the one hand, new welding methods, welding equipment and welding materials should be developed to further improve the welding quality and safety and reliability, such as improving the existing welding energy sources such as arc, plasma arc, electron beam and laser; Using electronic technology and control technology, improve the process performance of the arc, and develop a reliable and light arc tracking method.
On the other hand, we should improve the level of welding mechanization and automation, such as the realization of program control and digital control of welding machines; Develop a special welding machine that automates the whole process from preparation process, welding to quality monitoring; In the automatic welding production line, the promotion and expansion of numerical control welding robots and welding robots can improve the welding production level and improve the welding health and safety conditions
Post time: Sep-02-2022